Malzeme özellikleri akış verimliliğini etkilemede önemli bir rol oynar. yiyecek ve içecek ambalajı enjeksiyon kalıbı yapımı. Akış verimliliği, erimiş plastik malzemenin kalıp boşluğuna ne kadar iyi aktığını ve enjeksiyon kalıplama işlemi sırasında kalıp boşluğunu ne kadar iyi doldurduğunu ifade eder. Farklı malzeme özellikleri bu hususu çeşitli şekillerde etkileyebilir. İşte nasıl:
1. Erime Akış Hızı (MFR) veya Erime Akış İndeksi (MFI):
- Akış Verimliliğine Etkisi: MFR veya MFI değeri yüksek olan malzemeler daha fazla akışkanlığa sahiptir, bu da kalıp boşluğuna daha kolay akabilecekleri anlamına gelir. Bu, tüm kalıp özelliklerini etkili bir şekilde doldurmak için iyi akışkanlığın gerekli olduğu karmaşık veya karmaşık kalıp tasarımları için avantajlıdır.
2. Viskozite:
- Akış Verimliliğine Etkisi: Viskozite, malzemenin akışa karşı direncinin bir ölçüsüdür. Düşük viskoziteli malzemeler daha kolay akarken, yüksek viskoziteli malzemeler daha yavaş akar. Düşük viskoziteli malzemeler kalıp boşluğunu daha hızlı ve daha az basınçla doldurarak akış verimliliğini artırır. Yüksek viskoziteli malzemeler daha yüksek enjeksiyon basınçları ve daha uzun dolum süreleri gerektirebilir.
3. Malzeme Sıcaklığı:
- Akış Verimliliğine Etkisi: Enjeksiyonlu kalıplama sırasında malzeme sıcaklığı kritik öneme sahiptir. Daha yüksek sıcaklıklar malzemenin viskozitesini azaltarak daha kolay akmasını sağlar. Ancak aşırı ısınma bozulmaya veya bükülmeye neden olabilir. Akış verimliliğini optimize etmek için uygun sıcaklık kontrolü şarttır.
4. Dolgular ve Takviyeler:
- Akış Verimliliği Üzerindeki Etki: Dolgu maddeleri (örn. cam elyafı) veya takviyeleri olan malzemelerin akış özellikleri değişmiş olabilir. Bu katkı maddeleri malzemenin akış davranışını etkileyebilir ve kalıbın uygun şekilde doldurulmasını sağlamak için proses parametrelerinin ayarlanmasını gerekli hale getirebilir.
5. Malzeme Sünekliği ve Esnekliği:
- Akış Verimliliği Üzerindeki Etki: Sünek ve esnek malzemeler, karmaşık kalıp geometrilerine daha kolay uyum sağlayarak karmaşık tasarımlarda akış verimliliğini artırır. Kırılgan malzemeler kalıp özelliklerini kusursuz bir şekilde doldurmada zorluk yaşayabilir.
6. Malzeme Yoğunluğu:
- Akış Verimliliğine Etkisi: Malzeme yoğunluğu akış verimliliğini bir dereceye kadar etkileyebilir. Düşük yoğunluklu malzemeler daha sıkıştırılabilir olabilir ve kalıp özelliklerine daha iyi akış sağlayabilir. Bununla birlikte, daha yüksek yoğunluklu malzemeler daha iyi yapısal dayanıklılık sağlayabilir.
7. Isıl İletkenlik:
- Akış Verimliliği Üzerindeki Etki: Malzemenin termal iletkenliği, enjeksiyondan sonraki soğuma hızını etkileyebilir. Hızlı soğutma, malzemeyi vaktinden önce katılaştırarak akış verimliliğini etkileyebilir. Tam dolumu sağlamak için soğutma hızlarını dengelemek önemlidir.
8. Malzeme Reolojik Özellikleri:
- Akış Verimliliği Üzerindeki Etki: Kayma hızı ve kayma gerilimi gibi reolojik özellikler, malzemelerin farklı akış koşulları altında nasıl davrandığını açıklar. Kaymayla incelme davranışı iyi olan malzemeler, yüksek kesme hızları altında daha az viskoz hale geldiklerinden gelişmiş akış verimliliği sergilerler.
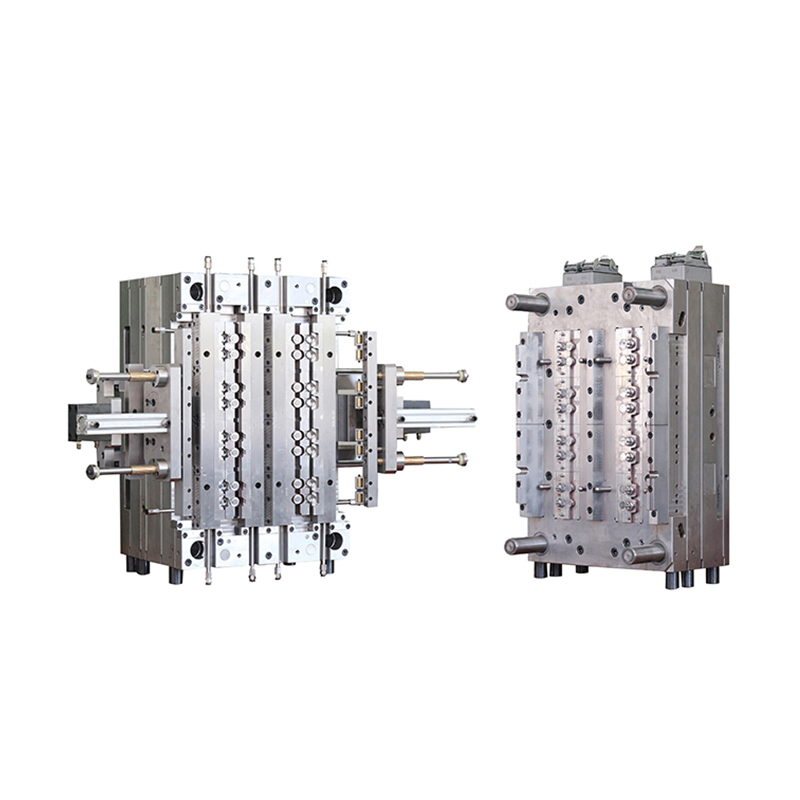
9. Malzeme Özellikleri (örneğin, Amorf ve Kristalin):
- Akış Verimliliği Üzerindeki Etki: Malzemenin spesifik yapısı, ister amorf ister kristal olsun, akış davranışını etkileyebilir. Amorf malzemeler daha düzgün ve izotropik bir akışa sahip olma eğilimindeyken, kristal malzemeler yönlü akış özellikleri sergileyebilir.
10. Malzeme Çarpılma Eğilimi:
- Akış Verimliliği Üzerindeki Etki: Soğutma sırasında bükülmeye eğilimli malzemeler, bükülmeye neden olan akış kesintilerini önlemek için daha yavaş enjeksiyon hızları veya daha dikkatli sıcaklık kontrolü gerektirebilir.
Yiyecek ve içecek ambalajı enjeksiyonlu kalıp yapımında akış verimliliğinin optimize edilmesi, belirli kalıp tasarımı ve üretim gereksinimleri için doğru özellik kombinasyonuna sahip bir malzemenin seçilmesini içerir. Ayrıca malzemenin düzgün bir şekilde akmasını ve kalıp boşluğunu kusursuz bir şekilde doldurmasını sağlamak için sıcaklık ve enjeksiyon hızı gibi proses parametrelerinin hassas kontrolünü gerektirir. Ayrıca kalıp tasarımı, verimli ve eşit dolum için malzeme akışını yönlendirmede kritik bir rol oynar.